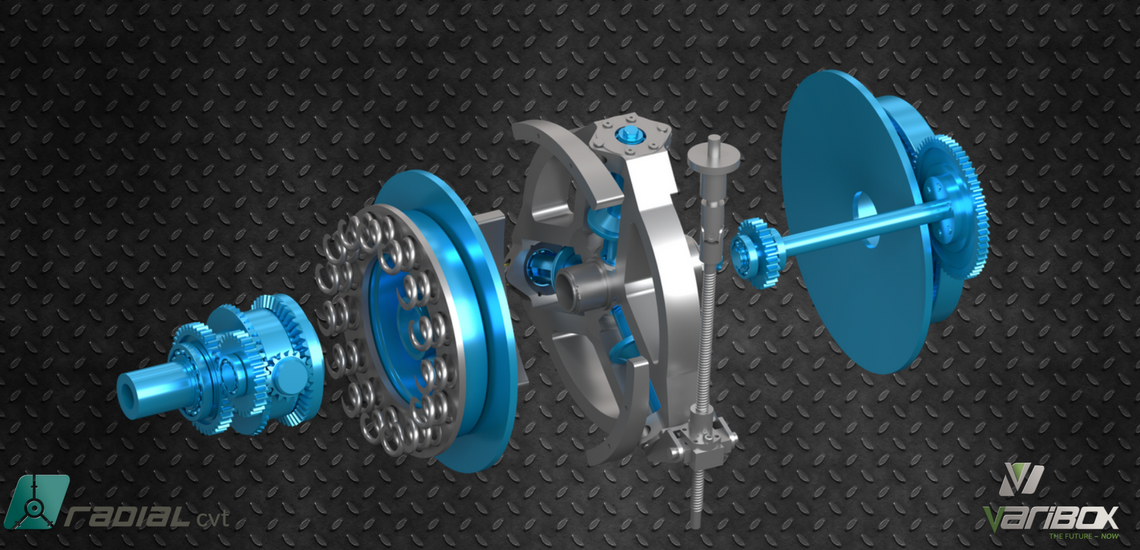
Application of the RADIALcvt in Pure Electric Vehicles
Growing global concerns over carbon emissions have resulted in the market share for electric vehicles (EVs), experiencing a rapid exponential growth. Bosch forecasts an increase in multiple ratios, coupled with sustained growth in market share and development for EVs in the next few years.
With the current drive towards electric vehicles, the optimization of various components contributing to overall energy efficiency of EVs is becoming more important. Innovations into higher energy dense batteries and other energy storing devices require that inefficient components that slow down advances in these developments be done away with.
A case in point is the primary power source in electric vehicles, the electric motor, which shares some common disadvantages with the internal combustion engine. One of these disadvantages is that both the electric motor and its drive/inverter, as well as the internal combustion engine are not equally efficient under different loads and speeds.
Single Speed
A fixed drive (single speed) in EVs has the lowest cost and is the least complicated, requiring at most a locking ring (dog clutch) to tow the vehicle in emergency conditions. This configuration however has no means to optimise the overall vehicle energy consumption as far as configuration between electric motor and wheels is concerned, other than the optimized selection of the fixed gear ratio between motor and wheels.
Multiple Stepped Speed
When multiple stepped ratios (two and three speeds and more) are considered, the following issues arise, and the solutions to these exponentially increase the complexity of the EV transmission if compared to the single speed case:
- All the reviewed work indicates that ratio change synchronisation with a single electric motor is not possible without a clutch (except the Oerlikon 4 speed high end
EV transmission which requires two motors). As a result, all the reviewed multi speed transmissions functions as an AMT (automated manual transmission) or as a DCT (dual clutch transmission) as in the case of the Antonov transmission, all using a clutch or dual clutch respectively.
- In order to realise above, a clutch system with automated clutch control is needed
- An automated ratio changing mechanism is also required.
The upside to a stepped multi speed is that high mechanical efficiency is maintained if compared to the single speed and that the electric motor is partially optimised in driving and regeneration conditions to provide energy consumption improvements up to about 15% compared to the single speed. It also allows for partial optimisation of the electric motor in terms of size, speed range and torque range.
Variable Mechanical Drives
All the reviewed work which considered CVT's/IVT's used existing well-known systems limited to toroidal and belt/chain CVT transmissions as well as these transmissions in IVT/power split configurations. These transmissions are characterised by the following disadvantages:
- Much lower mechanical efficiency than a fixed ratio.
- All require a hydraulic control system.
- They are heavy and expensive.
- All toroidal and belt/chain CVT include an overdrive in their ratio range (output turns faster than the input) thus additional reduction gearing would be needed in electric vehicle implementation.
On the upside, these transmissions provide the following advantages:
- Fully optimise the electric motor in driving and regeneration conditions.
- Provide better vehicle acceleration and gradient ability.
- A definite potential to provide better energy consumption than stepped transmission if its mechanical efficiency is within certain limits.
- They do not require a clutch, but only a locking ring/dog clutch, the same as for the single speed.
The RADIALcvt as an Ideal Electric Vehicle Transmission
Although the RADIALcvt mechanical efficiency is at most within an estimate of about 3% less than the stepped transmissions it is however much more compact lengthwise than the stepped transmission with a clutch or dual clutch.
The various cited CVT simulations proved the advantages of a CVT transmission in pure electric vehicles, but the low overall efficiencies of current commercial CVT's in some cases eroded all the advantages away.
The RADIALcvt thus provides an excellent solution to pure electric vehicles, because of its simplicity and fundamental advantages with very high mechanical efficiency.
Please download the full RADIALcvt simulation document at http://www.varibox.com/media/1177/radialcvtdesignver16.pdf.
Above document provides all details from which above parameters were obtained.
A full detailed version of this article can also be downloaded at http://www.varibox.com/media/1184/radialcvtelectricver14.pdf
This document includes all the references and sources and provides a very detailed analysis.